

Which are essential for good performance. Numbers of more than 500`000, which is sufficient to achieve high L/D ratios, Together with the available gearboxes, this lead to local Reynolds Mach number was limited to 0.3, as a compromise between aerodynamics and noiseĬonstraints. To occur at maximum diameter, but on the other hand the tip Mach number isĭirectly proportional to the diameter for a fixed velocity of rotation. On the one hand, simple momentum theory correctly predicts maximum efficiency
#Airfoil design full#
A lower loading would increase the full power times, but was not Power and non operating times, a specific power loading of 450 W/m² had been To achieve high yearly power on times, with short low Regarding low manufacturing costs and competitive energy costs, the number ofīlades was limited to two. To stall sharply when the operating limits are exceeded, thus limiting theĪfter some preliminary design studies, the parameters for the design, (such a windmill has no variable pitch blades toĬontrol the mill at higher wind speeds instead, the airfoils are designed Wind speeds, it was decided to direct the aerodynamic layout towards a To avoid destruction of the windmill due to over speed caused by high A gearbox between power generatorĪnd the rotor of the windmill permitted the decoupling of aerodynamics and Switched between two velocities of rotation and that the blade angle
#Airfoil design generator#
Parameters of the windmill were a constant speed generator which could be Proposed by the manufacturer, based on market studies. Inverse design method for the airfoil sections.įor a small horizontal axis wind turbine, the main project data were The final blade geometryĬan be tailored exactly to the desired main operating range by using a suitable Vortex lattice methods lead to quite accurate results. Under off-design conditions, simple blade element methods and more complex

Windmill, as defined by Glauert and Prandtl during the 1920s. Results, using inverse design methods, based on the minimum induced loss Today, the design of horizontal axis windmills can be performed with good The airfoils have been designed using direct inverse design methods. Were part of the design of an optimum windmill. 219–221, 1977.Airfoils for Windmills Aerodynamic Design of a Windmill Introduction Ramamoorthy, P., and Padmavathi, K., Airfoil Design by Optimization, Journal of Aircraft, vol. A., Wing Design by Numerical Optimization, Journal of Aircraft, Vol. R., Dot Users Manual, VMA Engineering, Goleta, Georgia, 1989. N., Numerical Optimization Techniques for Engineering Design, McGraw-Hill Book Company, New York, New York, 1984. Martinelli, L., Jameson, A., and Grasso, F., A Multigrid Method for the Navier-Stokes Equations, AIAA Paper 86-0208, 1986. 216–224, 1991.īirckelbaw, L., Inverse Airfoil Design Using the Navier-Stokes Equation, Proceedings of the AIAA 7th Applied Aerodynamics Conference, Seattle, Washington, pp. N., Airfoil Design Method Using the Navier-Stokes Equations, Journal of Aircraft, Vol.
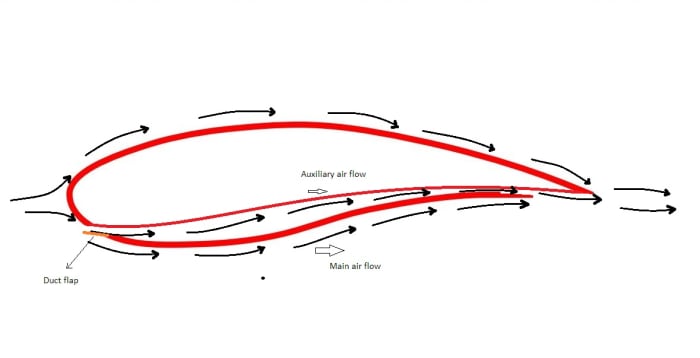
Hirose, N., Takanashi, S., and Kawai, N., Transonic Airfoil Design Procedure Utilizing a Navier-Stokes Analysis Code, AIAA Journal, Vol. D., and Eyi, S., Transonic Airfoil Design by Constrained Optimization, Proceedings of the AIAA 9th Applied Aerodynamics Conference, Baltimore, Maryland, Vol. D., and Eyi, S., Aerodynamic Design via Optimization, Proceedings of the 17th ICAS Congress, pp. Haüser, Pineridge Press, Swansea, England, Vol. Y., Numerical Optimization Design of Transonic Airfoils, Numerical Methods in Laminar and Turbulent Flow, Edited by C. K., Design Using Euler Equations, AIAA Paper 84-2166, 1984.Ĭhen, M. N., Efficient Algorithm for Numerical Airfoil Optimization, Journal of Aircraft, Vol., 16, pp. B., and Drela, M., Two-Dimensional Transonic Aerodynamics Design Method, AIAA Journal, Vol. E., The Design of Transonic Airfoils by a Well-Posed Inverse Method, International Conference on Inverse Design Concepts in Engineering Sciences, Austin, Texas, 1984.
